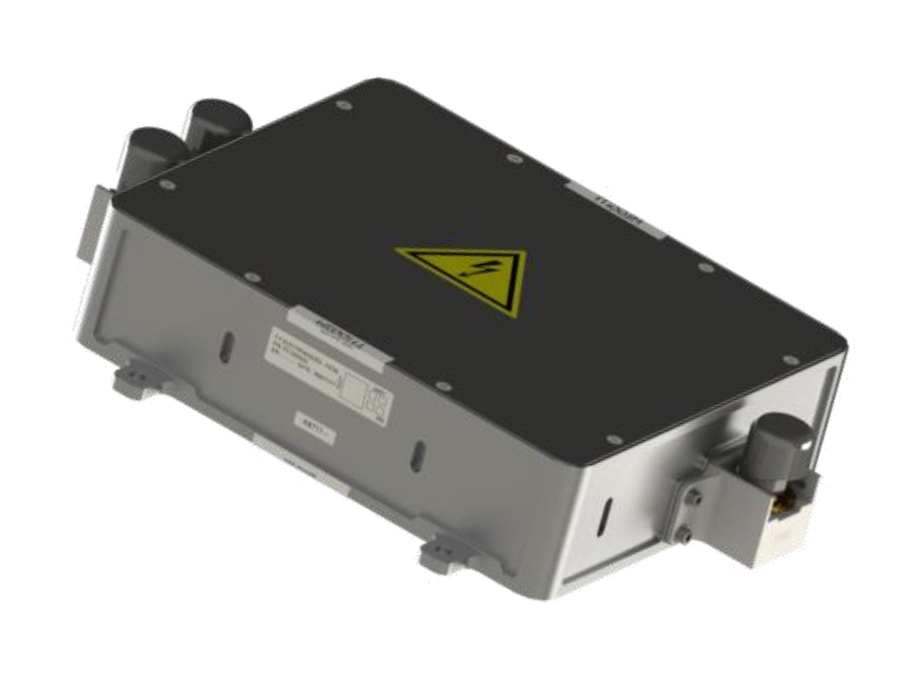
The PCC controls the transient starting torque provided by the DC machine to the engine.
- Maximum torque is no longer dependent on electrical source, battery temperature, wiring…
- Applied torque is a slope (no longer a step) to avoid any shaft transient oscillation leading to high torque overshoot (up to 2X in case of poor damping)
- Provides smooth starting torque
- Accurate control of the peak torque provided by the S/G or the starter
- Limits transient under-voltage on HC DC Bus thanks to inrush current limiting
- In order to optimize the volume of DC/DC converter, we choose DIRECTFET Technology withwith Cooled Direct FETTM on PCB
- Control : mixed analog + CPLD
- Efficiency > 90%
Key features
- 3 phases 115 Volts alternating current(VAC)-variable frequencypower input
- Active power factor corrector
- Sensorless motor drive
Applications
- Airbus civil aircraft
- Boeing civil aircraft
Specifications
Electrical
Input voltage
V= 10 to 32 VDC
Output current
500 A
Starting Duration
Three consecutive starts without rest time
High switching frequency (>150 Khz)
Standard protection (short circuit, overheating, overvoltage, EMI)
High switching frequency (>150 Khz)
Standard protection (short circuit, overheating, overvoltage, EMI)
Physical
Width
200 mm
Height
60 mm
Depth
150 mm
Weight
1 900g
Environmental
Temperature
-45°C to +70°C (normal operating conditions)
Certification approvals
ABD 100
EN 2282
DO 160- sect 10
EN 2282
DO 160- sect 10
Note: Due to continuous process improvement, specifications are subject to change without notice